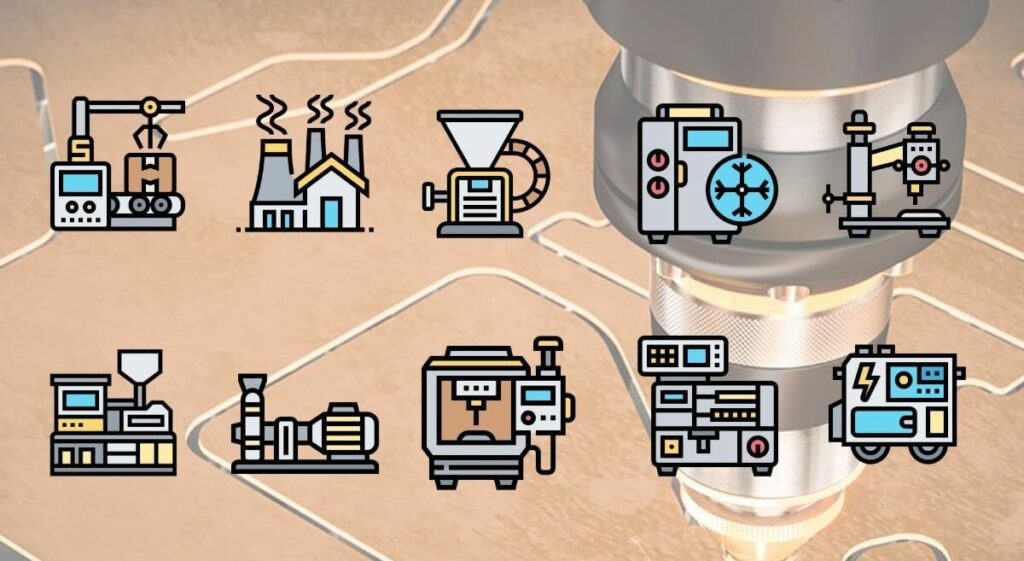
Métodos de Fabricação | Inteligência de Produção
São utilizados vários métodos na técnica de produção que podem ser por meio de eletrólise, vacum forming, eletroerosão, usinagem e injeção, que são os mais conhecidos. Basicamente todos os materiais produzidos podem ser formatados pelo processos de fabricação, que veremos a seguir.
Conformação
Ato de conformar o material produzido é dizer que concebemos o produto por processos industriais ou manuais que resultarão em um objeto com características que foram concebidas para alguma finalidade, é modificar o material para outro. Podemos classificar em:
- Estado Líquido – é quando derrete-se uma matéria prima e se despeja em fôrmas, para que seja transformado em uma nova peça.
- Estado Plástico – é quando a peça está no seu estado viscoso.
- Estado Sólido – é quando o material está endurecido após passar pelo estágio líquido e já estar moldado no formato que se quer imprimir ao objeto.
Corte na produção
O corte é todo processo que demanda o uso de lâminas cortantes, laser, tesouras ou sistemas de guilhotinas que ao ser impulsionadas em direção ao material, vai produzir a ruptura e separação em partes, que pode ser em tamanhos padronizados ou diferentes, mas o suficiente para atender ao pedido.
No processo de fabricação é fundamental que a peça, vez ou outra, acabe passando nesse setor, toda vez que se queira produzir o fracionamento da mesma, visando diminui-la ou no término do acabamento final.
O corte se divide em quatro categorias, a saber:
- Corte de chapas – fracionar algo plano como chapa de papelão, por exemplo, que ao passar nas guilhotinas tem seu fracionamento em partes ou seções.
- Corte com formação de cavacos – refere-se ao corte efetuado que resulta em sobras de material da peça e é muito comum nos processos de usinagem.
- Corte sem formação de cavacos – resultado de um corte que não desprende qualquer pedaço ou fração que gere respingos do material da peça.
- Corte a laser/tocha – é produzido com sistema de corte laser, também conhecido como tocha.
Junções ou Uniões
Dentro do processo de produção, usamos ainda outro sistema amplamente conhecido, que é a junção ou união. Ocorre quando usamos dois ou mais tipos de materiais na elaboração da mesma peça, quando se mescla os elementos diferentes entre si.
Podemos classificar em:
- Junção térmica – processo que se enquadra em aquecer o material com intuito de que ele grude um elemento no outro por meio desse processo de aquecimento ou por ultrassom.
- Junção adesivos - utilização de tipos específicos de cola onde permite que as peças sejam unidas, respeitando o tipo do adesivo que faça adesão ao tipo de material empregado.
- Junções mecânicas – configura-se basicamente no uso de pregos, tachas, parafusos, rebites que serão utilizados para agregar uma parte na outra.
Acabamentos nos métodos de fabricação
Dentro do método de fabricação, chamamos de acabamento do material a finalização da peça produzida. É a última etapa para que possa depois passar pelo controle de qualidade. A logística desses itens permite ao controlador de produção, visualizar todo a cadeia de produção, do início ao fim e de encerrar o ciclo para novo reinício sempre que necessário.
São classificadas em:
- Abrasão/corte – processo que visa lixar a peça de modo que a mesma não tenha rebarbas que deixem as superfícies cortantes.
- Recobrimento – processo de pintura que pode ser o uso de tintas spray que vai ser espalhada no corpo da peça.
Hoje ficamos por aqui e espero sua leitura tenha sido produtiva. Até uma próxima edição, onde daremos continuidade em mais processos interessantes da cadeia de produção.